L'asphalte est un mélange multicomposant pour la fabrication de sable et de pierre. Pour acquérir des propriétés astringentes, des composants bitumineux sont ajoutés à la substance. Appelez correctement cette composition asphalte. Cependant, même dans des publications spécialisées, utilisez le terme "asphalte", ce qui n’est pas une erreur.
Premières routes pavées
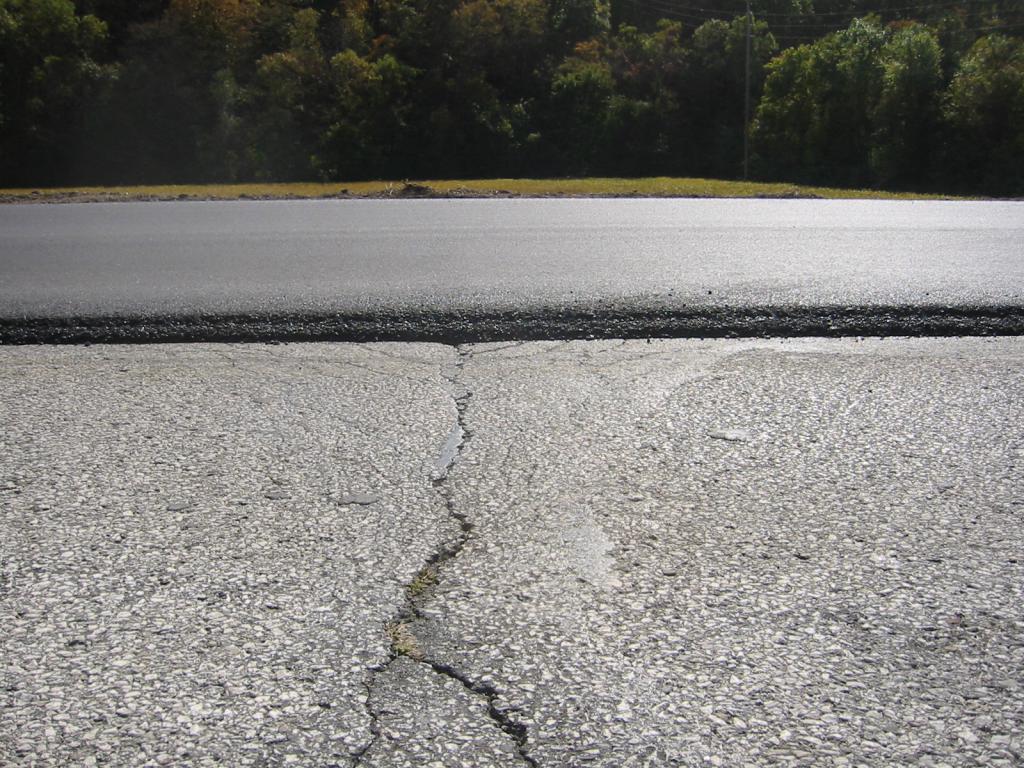
Pour la première fois, des chaussées en asphalte ont été utilisées à Babylone (environ 600 ans av. J.-C.). Le bitume pour créer un revêtement dur a été extrait des roches. Après la destruction de l'ancienne civilisation, la construction de la route à l'aide de matériaux bitumineux n'a repris qu'au 19e siècle en Europe occidentale. Ensuite, la technologie a été activement utilisée aux États-Unis. Dans ce cas, le revêtement d'asphalte était constitué de roches contenant du bitume, broyées à l'état de poudre. Ce revêtement est appelé «asphalte bourré».
L'apparition de l'asphalte en Russie
Dans notre pays, l'asphalte a commencé à être fabriqué en 1869 à partir d'asphalte de Syzran. À la différence de l'asphalte tassé étranger, la surface de la route de l'empire russe était constituée d'un mélange fondu contenant du gravier et du sable, du bitume et de l'asphalte. L'asphalte préparé a été jeté sur le sol et nivelé à l'aide d'un outil à main. De plus, la route a été écrasée par une charge massive. Les experts appellent cette technologie "asphalte pavé". Depuis 1906, du bitume de pétrole y a été ajouté.
Au début du XXe siècle, des scientifiques ont proposé des mélanges spéciaux d’asphalte, qui ont progressivement commencé à déloger les revêtements damés et coulés. Les principaux avantages des nouveaux articles sont que la préparation du revêtement, son application et son compactage ont été réalisés de manière entièrement mécanique sans travail manuel. En URSS, le premier tronçon de route en béton bitumineux est apparu sur la route de Volokolamsk en 1928, grâce aux efforts du professeur P.V. Sakharov.
Avantages du béton bitumineux
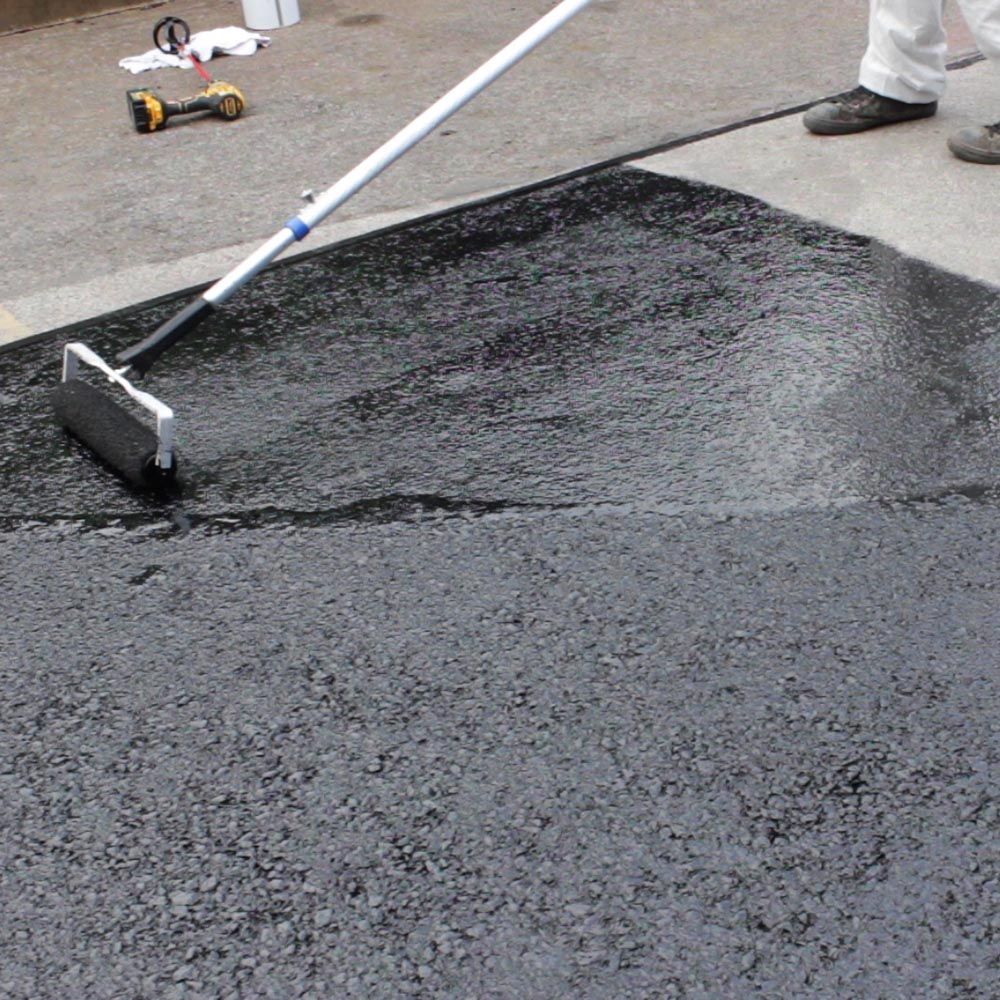
De nos jours, plus de 60% de la longueur totale des routes en Russie sont constituées de chaussées en béton bitumineux. Cette popularité du matériau pour l’aménagement de la route est due aux avantages suivants:
- Usure lente.
- Haute résistance à la charge.
- Résistance aux changements de température et d'eau.
- Démontage facile et nettoyage.
- La possibilité d'utiliser le matériel à nouveau.
- Réduction des vibrations lors de la circulation sur la route.
Le fonctionnement de la chaussée en béton bitumineux vise à réduire les vibrations créées par le mouvement de véhicules automobiles lourds. Une telle chaussée permet de réduire le bruit des roues et contribue également à un mouvement fluide et calme du flux de voitures.
La construction de routes à partir de chaussées en béton bitumineux peut être réalisée par la méthode de la vitesse d'écoulement utilisant un processus mécanisé intégré.
Le béton bitumineux est posé sur la route avec une pente ne dépassant pas 60%. Sur des pentes supérieures à 40%, le revêtement est rendu rugueux afin de fournir une traction suffisante sur les pneus du véhicule. La pente transversale de l'asphalte doit être comprise entre 15 et 20%.
Utilisation du mélange de goudron
Il est beaucoup moins courant pour la construction de chaussées en béton bitumineux d’utiliser des mélanges de goudron, dans la composition desquels du goudron de houille est ajouté pour la viscosité. Le revêtement de ce type en apparence ne diffère presque pas du béton bitumineux classique.Le mélange de goudron est plus résistant à l'usure, il est détruit plus rapidement par les températures extrêmes et par l'eau. En outre, il s'efface rapidement sous l'influence des pneus en caoutchouc des véhicules.
Le taux de béton est interdit dans les villes, car l'évaporation de fractions légères de goudron est nocive pour l'homme. De plus, sous l'influence de l'eau, les phénols sont imbibés d'asphalte nocif pour l'homme et l'environnement.
Composition d'asphalte
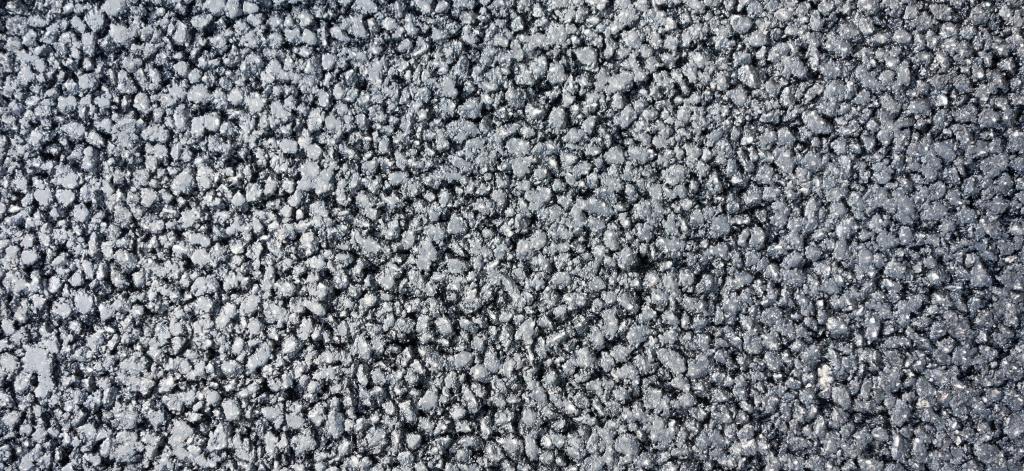
Beaucoup sont intéressés par un dispositif de revêtement d'enrobés bitumineux. Les principaux composants de la couche supérieure de la route sont le bitume, le sable, les variétés de gravier et le gravier. Des charges et des composants minéraux sont également ajoutés à certaines variétés pour donner au mélange une résistance accrue.
Le sable entrant dans la composition du revêtement de béton bitumineux joue le rôle de charge qui est nécessaire pour obtenir une pression uniforme du mélange sur le sol pendant la pose et la solidification. Sans sable, la route se serait étendue et du gravier aurait rampé. Dans certaines compositions spéciales, du ciment est ajouté, ce qui, avec le sable, donne au revêtement une dureté supplémentaire.
En tant que charge minérale dans la construction de revêtements en béton bitumineux, la roche concassée avant la formation de poussière est utilisée, par exemple le calcaire, la craie ou le grès. Il est conçu pour combler les petits vides lors de la pose sur route. Le grès est le plus polyvalent, car il est inerte à tout produit chimique. La craie et la chaux sont généralement utilisées sur les routes publiques. Du grès est ajouté lors de la construction de routes à proximité d'usines chimiques.
Des morceaux de caoutchouc ajoutés à l'asphalte et dont le diamètre ne dépasse pas 1,5 mm donnent l'élasticité et la résistance du revêtement à l'eau. Les chaussées en béton bitumineux contenant suffisamment de caoutchouc ont rarement tendance à se fissurer. Cependant, ce matériel est excessivement coûteux et son utilisation est donc souvent irrationnelle. En règle générale, une charge de caoutchouc est ajoutée lors de la construction de lignes à grande vitesse.
Classification
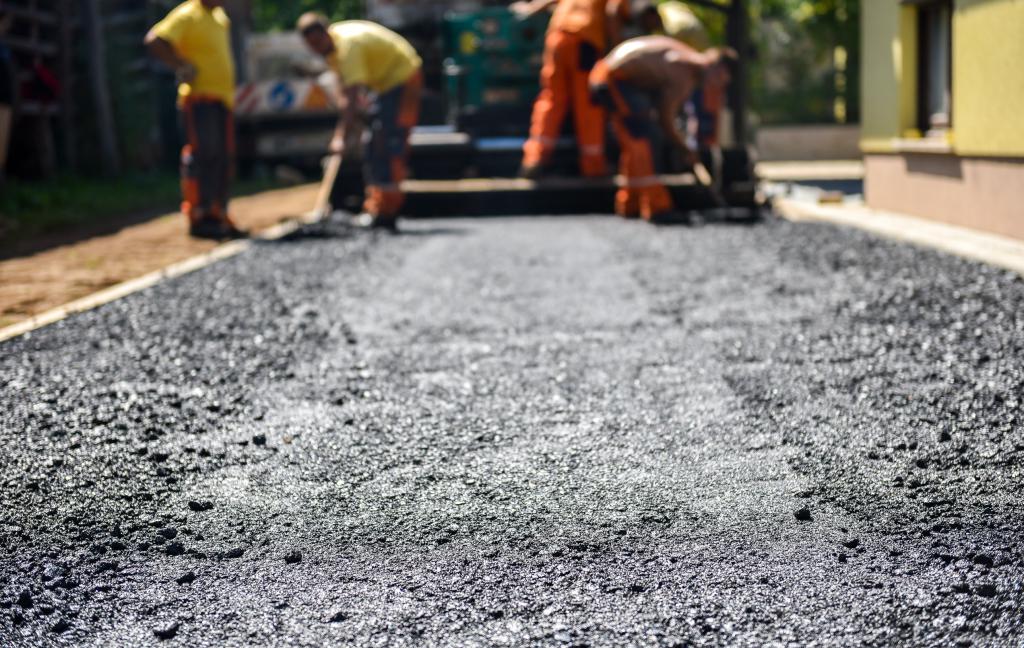
L'un des principaux paramètres du dispositif de revêtement en béton bitumineux est la taille de la pierre concassée entrant dans sa composition. Sur cette base, le mélange est divisé en plusieurs groupes:
- Mélanges denses. Ils sont utilisés lors de la pose de la couche supérieure de la chaussée en béton bitumineux. Un tel asphalte contient du gravier fin. Lors de la construction d'autoroutes conçues pour la circulation de véhicules légers (vélos et poussettes), ainsi que pour les piétons, des pierres concassées d'un diamètre maximal de 5 mm peuvent être utilisées. Des fractions plus grandes (jusqu'à 15 mm) peuvent être empilées sur les routes pour le déplacement des véhicules de tourisme uniquement.
- Mélanges poreux - c'est la meilleure option pour le dispositif de revêtement en béton bitumineux, où les véhicules de fret se déplaceront. En règle générale, il est utilisé lors de la pose initiale sur le sol ou le gravier. La composition de l'asphalte diffère de la densité en ce qu'une petite quantité de bitume y est ajoutée.
- Les mélanges très poreux sont la meilleure option pour la pose et la réparation de chaussées en béton bitumineux sur des routes à fort trafic, en particulier si des véhicules lourds et encombrants circulent sur des routes. Pour produire ce type d'asphalte, du gravier grossier (jusqu'à 40 mm) est ajouté au mélange. De telles dimensions permettent une bonne perméabilité à l'eau. Cette propriété est particulièrement utile dans les endroits où il est nécessaire de créer un drainage, par exemple dans les zones marécageuses ou dans les basses terres.
Fabrication d'asphalte
La technologie des revêtements en béton bitumineux consiste en la préparation des matières premières, leur mélange et leur chauffage simultané à haute température, ainsi que le stockage de l'asphalte obtenu dans un bunker chauffé spécial.
Lors de la réparation ou de la construction de la route, il est important que l’usine soit située aussi près que possible du site d’installation, car les matériaux de construction doivent être chauds.Si l'asphalte refroidit, il sera difficile de le compacter et la route résultante deviendra rapidement inutile.
Préparation des composants
Avant de commencer la production d'asphalte, le matériau préparé est séché et tamisé. Le sable, les roches et la pierre concassée entrent en production le plus souvent à l'état humide. La présence d'eau dans la composition menace de réduire les caractéristiques de résistance du futur asphalte, ainsi que par pulvérisation du mélange de bitume chauffé à haute température lorsque de l'humidité y pénètre.
Tous les matériaux fournis à l'usine sont séchés à une température de 150 degrés. Le dépistage est effectué à l'aide d'un écran. La charge minérale est broyée dans un moulin à poudre. Selon la technologie, le séchage peut être simple ou double. L'élimination de l'humidité peut se produire après le tamisage et le broyage.
Mélange de composants traités
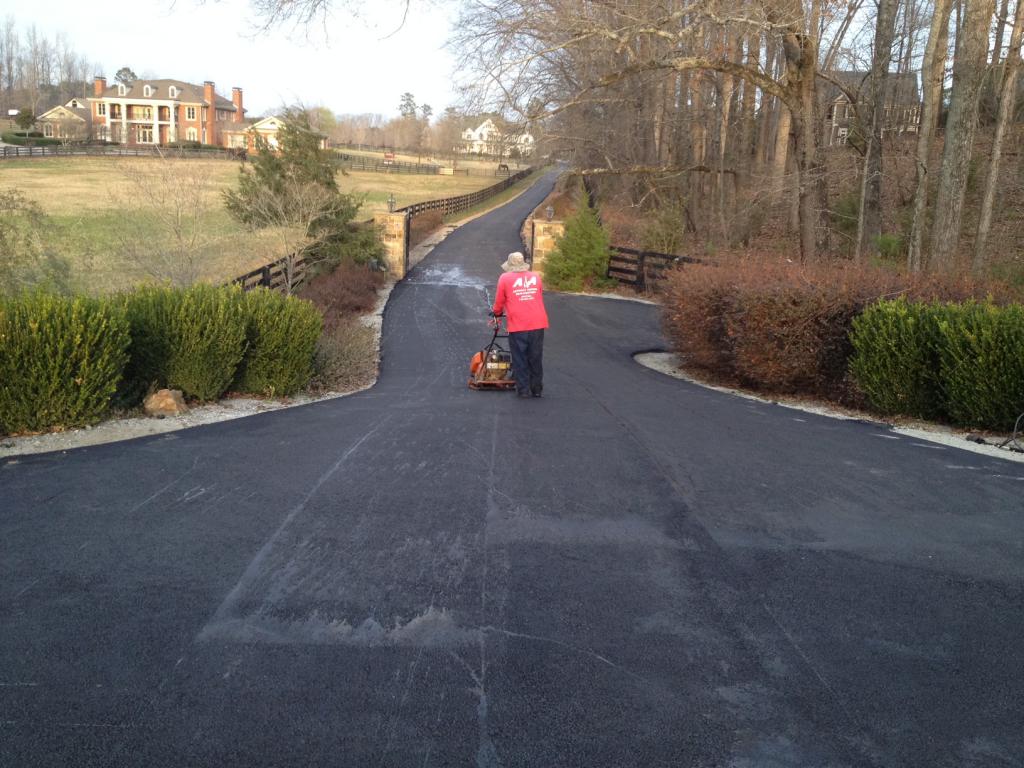
La pierre concassée et le sable après le traitement préliminaire tombent sur le convoyeur, d'où ils sont transportés vers la trémie, puis mélangés avec du bitume. Après cela, la température dans la trémie est augmentée à 160 degrés et le contenu est laissé à l’état chauffé pour être stocké pendant 4 jours maximum. Si, pendant cette période, le matériau n’est pas expédié au consommateur, il perdra ses caractéristiques de résistance.
Des additifs dans l'asphalte et le caoutchouc granulé sont ajoutés au mélange fini et chauffé, ce qui confère au matériau une résistance supplémentaire et une résistance aux facteurs externes.
Livraison d'asphalte sur le lieu de pose
Le béton bitumineux est transporté par route jusqu'au lieu d'installation ou de réparation de la chaussée en béton bitumineux. Le plus souvent, ce matériau de construction est transporté sur des camions à benne basculante ayant un corps résistant aux composants chauds. Pour le transport de la chaussée en béton bitumineux sur de longues distances, on utilise des kochers (voitures équipées de conteneurs permettant d'économiser de la chaleur). En eux, l'asphalte conservera sa température initiale pendant deux jours après le chargement.
Contrôle de la qualité de la route
Le béton bitumineux doit être conforme aux normes GOST et SNiP adoptées dans notre pays. Un certificat de conformité aux documents réglementaires n’est délivré au fabricant qu’après des tests complets.
Il existe plusieurs laboratoires en Russie qui surveillent la qualité des routes. Ils procèdent à l'échantillonnage du revêtement en béton bitumineux fini et en vérifient la conformité avec divers paramètres.
Dans les études, un échantillon moyen est tiré de la masse totale de béton bitumineux. Une analyse de la route déjà construite est réalisée en examinant le noyau (le noyau dit asphalte). Il est obtenu en perçant la base d’une chaussée en béton bitumineux à l’aide d’un foret creux spécial.
Application d'asphalte à froid
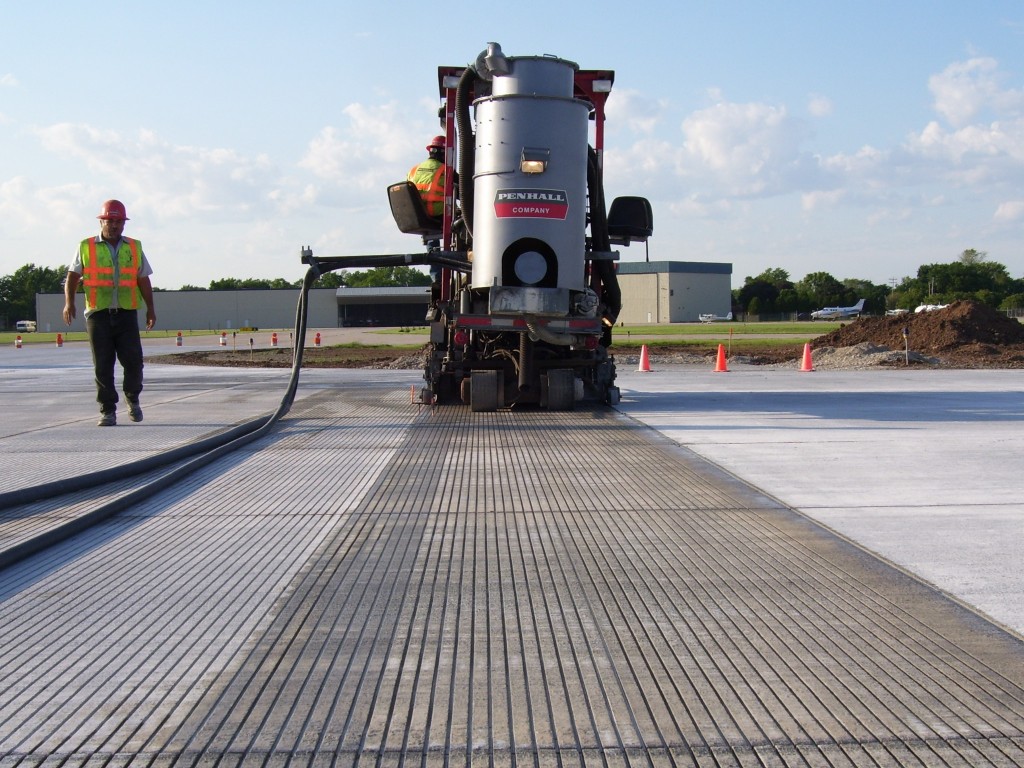
Dans les endroits où la livraison de matériaux de construction chauds pour la réparation ou la construction de la voie est impossible, on utilise une pose à froid de la chaussée en béton bitumineux. La technologie de cette construction routière se caractérise par des températures de fonctionnement plus basses pour chauffer le mélange (l’asphalte est chauffé à 100 degrés). Pour donner à la chaussée une résistance suffisante, des compositions de polymères sont utilisées.
Avant la pose, les travailleurs chauffent non seulement le béton bitumineux, mais également le lieu de la pose prévue. Selon la variété, la route peut être faite même avec le gel.
Un des avantages de la pose à froid est la longue durée de vie du matériau pour la construction de routes. Contrairement au béton bitumineux ordinaire, un bitume résistant au gel peut être posé après quelques semaines. Cependant, ce matériau présente des inconvénients importants, à savoir:
- La force est inférieure à 2 fois, comparée au mélange d'asphalte classique.
- Le matériau a un prix élevé en raison de l'ajout de composants protecteurs supplémentaires à sa composition.
- La technologie de pose est compliquée, ce qui entraîne une augmentation du coût de la chaussée.
- Ne supporte pas les lourdes charges.Il est interdit de conduire des véhicules pesant plus de 3,5 tonnes.
Une plaque vibrante est utilisée pour pilonner l'asphalte froid et la pose finale a lieu après un moment où, pendant l'opération, les voitures se déplaceront le long de la route finie, écrasant ainsi le revêtement.
Réutiliser l'asphalte
Le coût élevé de la construction de routes a conduit les experts à trouver des moyens d’économiser de l’argent. Un moyen de réduire les coûts de réparation et de construction des autoroutes est le recyclage, c'est-à-dire le recyclage du vieil asphalte en vue de sa réutilisation. La surface de la route reprend une seconde vie après avoir traité le matériau dans des recycleurs spéciaux mobiles.
Quel âge a l'asphalte est recyclé
Le traitement de l'asphalte pour obtenir un nouveau mélange pour la construction de routes est un processus de haute technologie. Pour produire un revêtement de haute qualité par recyclage, vous devez:
- Couper le vieux trottoir avec un remixeur. Un tel équipement enlève en douceur une couche de la route avec un cutter spécial.
- Broyer la couche broyée à la taille de la pierre concassée. Le matériau résultant est appelé un «granulateur». Il est utilisé pour réparer les routes et préparer d'autres mélanges de construction.
- Chauffez le four pour faire fondre le granulateur. Vous ne devez pas utiliser de source de feu ouverte, vous risqueriez une explosion.
- Ajoutez du bitume et divers additifs au four, si cela est prévu par la technologie de production du nouvel asphalte.
Une technologie telle que le recyclage est utilisée, en règle générale, pour la construction de routes dans la ville. L'asphalte recyclé a les mêmes propriétés que le nouvel, mais son prix est beaucoup plus bas.
Amélioration de la chaussée
Les revêtements de route peuvent être modernisés au fil du temps. L'une de ces méthodes est l'application de mastic sur l'asphalte. Le matériau de renforcement comprend du bitume et des polymères de caoutchouc liquides.
En cours de fonctionnement, des fissures apparaissent sur les routes où l'eau peut pénétrer. Lorsqu'il est gelé, l'asphalte est détruit, ce qui conduit à la formation de grandes fosses. Si vous appliquez le mastic à temps pour éliminer les fissures, vous pouvez prolonger la durée de vie de l'asphalte de plusieurs années.
Avantages et inconvénients de l'asphalte
Le revêtement d'asphalte pour le trafic est utilisé depuis plusieurs décennies. Il n'y a pas encore de remplaçant pour lui, et voici pourquoi:
- Le revêtement en asphalte n'est pas très coûteux, surtout si la route est conçue pour un transport léger.
- L'asphalte résiste aux gelées, n'a pas peur de l'humidité et des fortes pluies, bien sûr, si ses technologies de pose sont appliquées.
- Si le revêtement s'est partiellement affaissé, vous pouvez le réparer en appliquant un patch.
- Dans les climats difficiles, la technologie de l'asphalte froid peut être utilisée.
Alternatives à l'asphalte
Dans le monde entier, les scientifiques travaillent à la création d'une alternative plus fiable et moins chère au mélange de béton bitumineux, mais aucun matériau de ce type n'a encore été jugé compétitif. De plus, le revêtement en asphalte est en constante modernisation. L’introduction généralisée de nouvelles substances polymères peut considérablement améliorer les propriétés de la surface de la route et élargir les limites de son application. Ceci est confirmé par de nombreux tests de laboratoire.
Construction en béton bitumineux
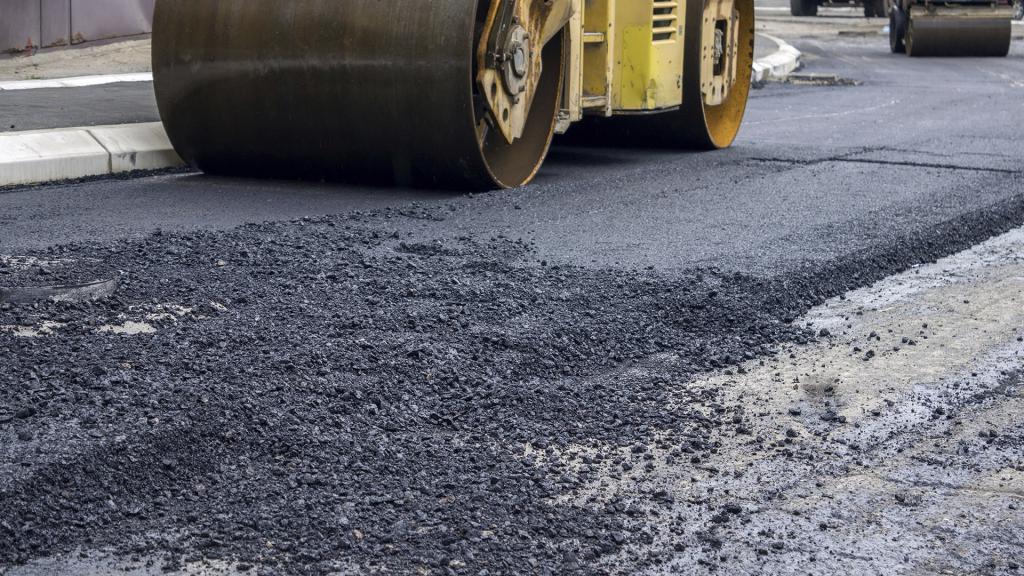
Les spécialistes s'efforcent de construire et de construire des routes de manière à ce qu'il y ait le moins possible de couches sur la chaussée, jusqu'à un. Le béton bitumineux doit de préférence être posé directement sur le sol. Le nombre minimum de couches réduit le temps de réparation de la toile, facilite l'organisation de la construction de nouvelles routes, réduit la variété d'équipements requis pour la pose d'asphalte.
La conception moderne de la chaussée en béton bitumineux comprend les éléments suivants:
- Couche supérieure.
- La couche inférieure poreuse.
- Pierre concassée mélangée à des liants.
- La base est faite de gravier ou de gravats.
- Couche de sable.
- Asphalte concassé.
Lors de la construction d'un revêtement en asphalte, un certain nombre de conditions doivent être respectées. Pour créer une liaison solide entre la couche supérieure d’asphalte et la base, un matériau résistant aux fissures est appliqué à partir de matériaux traités au bitume d’une hauteur minimale de 15 cm.