El asfalto es una mezcla multicomponente, para cuya producción se utilizan arena y piedra. Para adquirir propiedades astringentes, se agregan componentes bituminosos a la sustancia. Llame correctamente a esta composición asfalto. Sin embargo, incluso en publicaciones especializadas utilice el término "asfalto", que no es un error.
Primeras carreteras pavimentadas
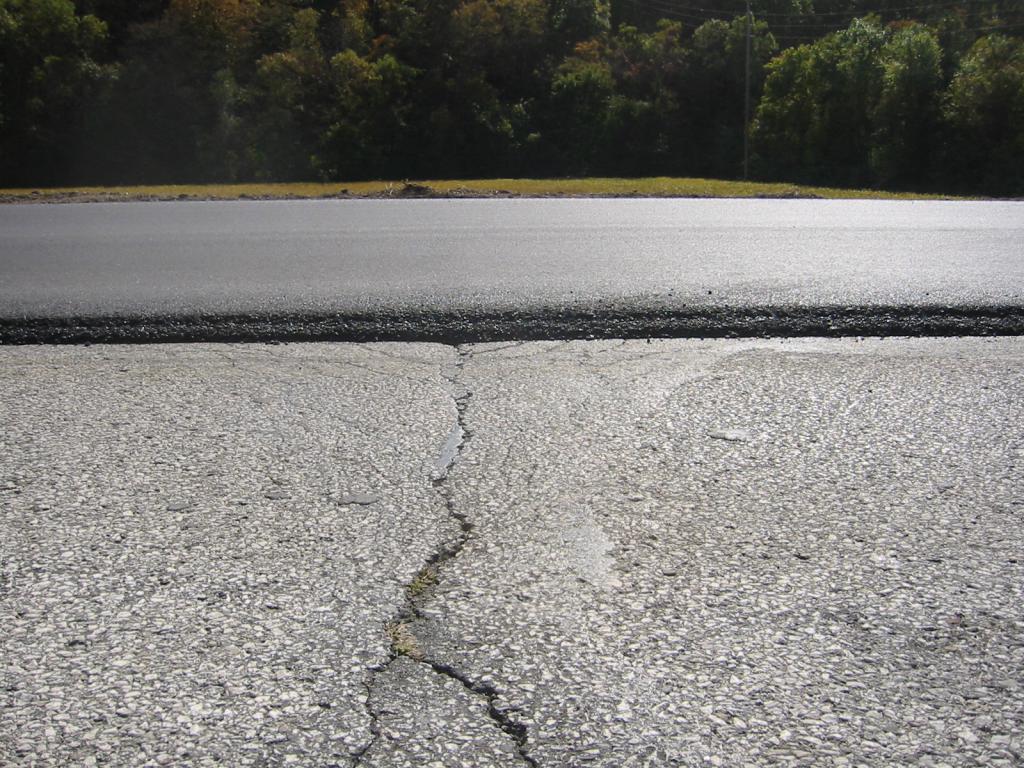
Por primera vez, se usaron pavimentos de asfalto en Babilonia (alrededor del año 600 a. C.). El betún para crear un recubrimiento duro se extrajo de las rocas. Después de que la antigua civilización fue destruida, la construcción de la carretera utilizando materiales de betún se reanudó solo en el siglo XIX en Europa occidental. Luego, la tecnología se utilizó activamente en los Estados Unidos. En este caso, el revestimiento de asfalto consistía en rocas que contenían betún, trituradas hasta un estado en polvo. Este recubrimiento se llama "asfalto apisonado".
La aparición de asfalto en Rusia
En nuestro país, el asfalto comenzó a fabricarse en 1869 a partir de rocas asfálticas de Syzran. A diferencia del asfalto apisonado extranjero, en el Imperio ruso la superficie de la carretera estaba hecha de una mezcla fundida, que contiene grava y arena, betún y roca de asfalto. El asfalto listo fue arrojado al suelo y nivelado con una herramienta manual. Además, el camino fue aplastado por una carga masiva. Los expertos se refieren a esta tecnología como "asfalto pavimentado". Desde 1906, se le añadió betún de petróleo.
A principios del siglo XX, a los científicos se les ocurrieron mezclas especiales de asfalto, que gradualmente comenzaron a desplazar los recubrimientos apisonados y fundidos. Las principales ventajas de los nuevos artículos consistieron en el hecho de que la preparación del recubrimiento, su aplicación y compactación se llevó a cabo en un modo completamente mecánico sin el uso de mano de obra. En la URSS, el primer tramo de carretera de hormigón asfáltico apareció en la autopista Volokolamsk en 1928 gracias a los esfuerzos del profesor P.V. Sakharov.
Ventajas del hormigón asfáltico
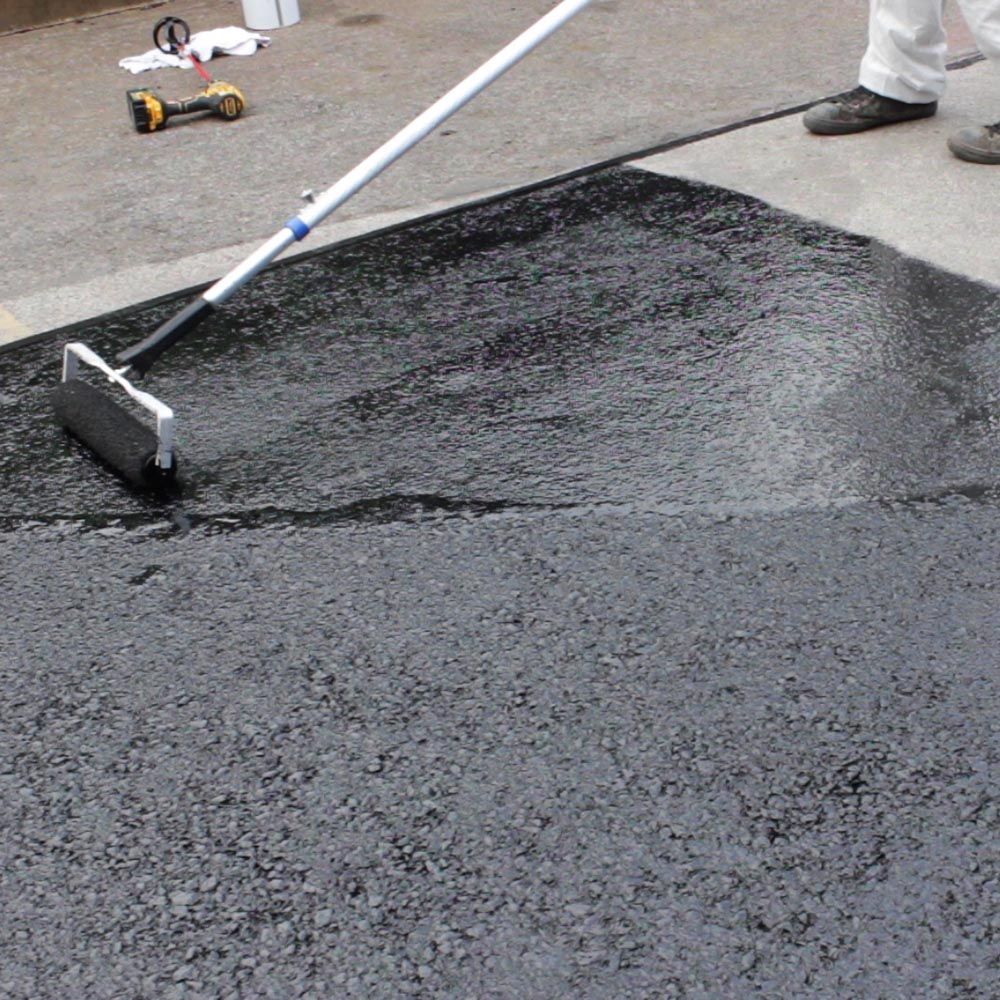
Hoy en día, de la longitud total de las carreteras en Rusia, más del 60 por ciento están hechas de pavimento de hormigón asfáltico. Tal popularidad del material para organizar el camino se debe a las siguientes ventajas:
- Desgaste lento.
- Alta resistencia a la carga.
- Resistencia a los cambios de temperatura y agua.
- Fácil desmontaje y limpieza.
- La capacidad de usar el material nuevamente.
- Vibración reducida durante el tráfico en la carretera.
La operación del pavimento de concreto asfáltico es para reducir la vibración que se crea como resultado del movimiento de vehículos pesados. Tal calzada permite reducir el ruido de las ruedas y también contribuye a un movimiento suave y tranquilo del flujo de automóviles.
La construcción de carreteras a partir de pavimento de hormigón asfáltico se puede llevar a cabo mediante el método de velocidad de flujo utilizando un proceso mecanizado integrado.
El hormigón asfáltico se coloca en la carretera con una pendiente de no más del 60 por ciento. En pendientes superiores al 40 por ciento, el revestimiento se endurece para proporcionar una tracción suficiente en los neumáticos del vehículo. La pendiente transversal del asfalto debe estar en el rango de 15-20 por ciento.
Uso de mezcla de alquitrán
Es mucho menos común que en la construcción de pavimentos de concreto asfáltico se utilicen mezclas de alquitrán, en cuya composición se agrega alquitrán de hulla para la viscosidad. El revestimiento de este tipo en apariencia casi no difiere del concreto asfáltico clásico.La mezcla de alquitrán es más resistente al desgaste, se destruye más rápidamente por las temperaturas extremas y el agua. Además, se borra rápidamente bajo la influencia de los neumáticos de goma de los vehículos.
Se prohíbe el uso de concreto en grados en las ciudades, ya que la evaporación de las fracciones de alquitrán ligero es perjudicial para los humanos. Además, bajo la influencia del agua, los fenoles se empapan de dicho asfalto, que son perjudiciales para los humanos y el medio ambiente.
Composición de asfalto
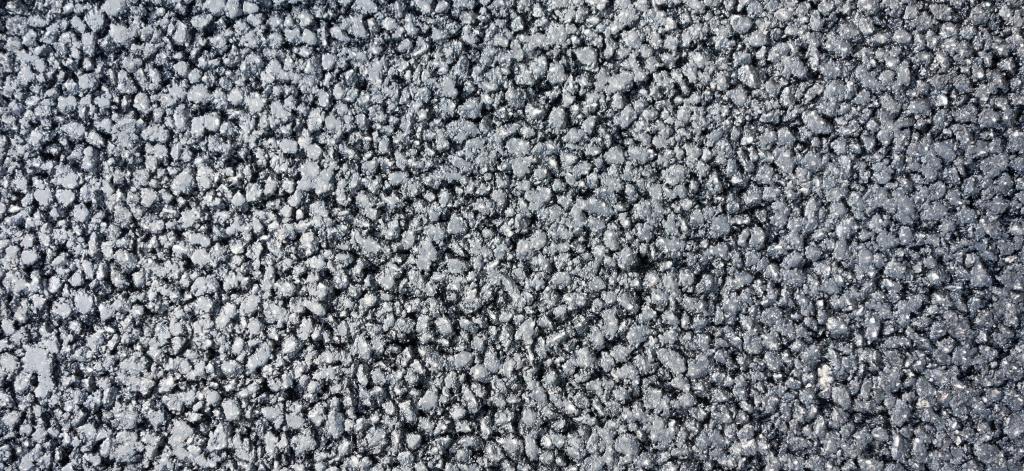
Muchos están interesados en un dispositivo para el recubrimiento de la mezcla de asfalto. Los componentes principales de la capa superior del camino son betún, arena, variedades de grava y grava. También se agregan rellenos y componentes minerales a algunas variedades para dar a la mezcla una mayor resistencia.
La arena en la composición del revestimiento de hormigón asfáltico desempeña el papel de una carga, que es necesaria para una presión uniforme de la mezcla en el suelo durante la colocación y la solidificación. Sin arena, el camino se habría extendido y la grava se habría arrastrado. En algunas composiciones especiales, se agrega cemento, que junto con la arena le da al recubrimiento una dureza adicional.
Como relleno mineral en la construcción de revestimientos de hormigón asfáltico, se utiliza roca triturada antes de la formación de polvo, por ejemplo, piedra caliza, tiza o arenisca. Está diseñado para llenar pequeños huecos durante el tendido de carreteras. La piedra arenisca es la más versátil porque es inerte a cualquier químico. La tiza y la cal se usan, por regla general, en las vías públicas. Se agrega arenisca durante la construcción de carreteras cerca de plantas químicas.
Se agrega miga de goma al asfalto con un tamaño de no más de 1.5 mm de diámetro para darle elasticidad al revestimiento y resistencia al agua. El pavimento de hormigón asfáltico con suficiente adición de caucho en su composición rara vez es propenso a agrietarse. Sin embargo, dicho material es excesivamente costoso, por lo que su uso es a menudo irracional. Típicamente, se agrega relleno de goma durante la construcción de líneas de alta velocidad.
Clasificación
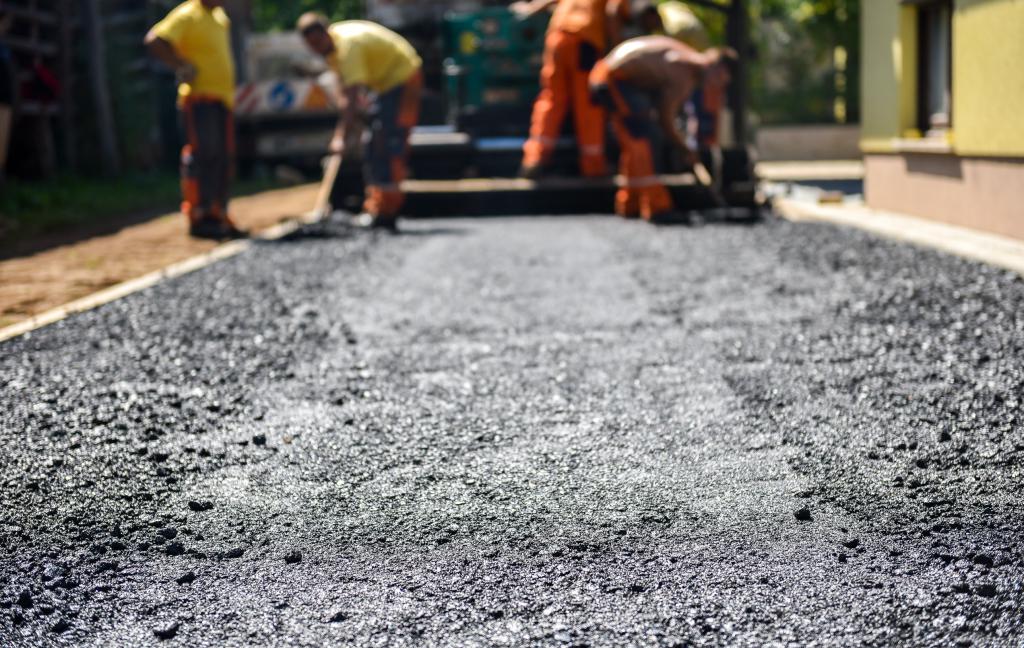
Uno de los parámetros principales en el dispositivo de pavimento de hormigón asfáltico es el tamaño de la piedra triturada utilizada en su composición. En base a esto, la mezcla se divide en varios grupos:
- Mezclas densas. Se utilizan durante la colocación de la capa superior del pavimento de hormigón asfáltico. Tal asfalto contiene grava fina. Durante la construcción de carreteras diseñadas para el movimiento de vehículos ligeros (bicicletas y cochecitos), así como para peatones, se puede utilizar piedra triturada con un diámetro de no más de 5 mm. Las fracciones más grandes (hasta 15 mm) se pueden apilar en carreteras para el movimiento de vehículos de pasajeros únicamente.
- Mezclas porosas: esta es la mejor opción para el dispositivo de pavimento de hormigón asfáltico, donde se moverán los vehículos de carga. Como regla general, se usa durante la colocación inicial en el suelo o la grava. La composición del asfalto difiere de la densa en que se le agrega una pequeña cantidad de betún.
- Las mezclas altamente porosas son la mejor opción para colocar y reparar el pavimento de concreto asfáltico en rutas de alto tráfico, especialmente si los vehículos pesados y voluminosos circulan por las carreteras. Para producir este tipo de asfalto, se agrega grava gruesa (hasta 40 mm) a la mezcla. Dichas dimensiones permiten una buena permeabilidad al agua. Esta propiedad es especialmente relevante en lugares donde es necesario construir drenaje, por ejemplo, en áreas pantanosas o en tierras bajas.
Fabricación de asfalto
La tecnología de los revestimientos de concreto asfáltico consiste en la preparación de materias primas, su mezcla y calentamiento simultáneo a alta temperatura, así como el almacenamiento del asfalto resultante en un búnker calentado especial.
Durante la reparación o construcción de la carretera, es importante que la planta se ubique lo más cerca posible del sitio de instalación, ya que el material de construcción debe estar caliente.Si el asfalto se enfría, será difícil compactarlo, y el camino resultante rápidamente dejará de tener valor.
Preparación de componentes
Antes de comenzar la producción de asfalto, el material preparado se seca y se tamiza. La arena, las rocas y la piedra triturada se producen con mayor frecuencia en estado húmedo. La presencia de agua en la composición amenaza con reducir las características de resistencia del asfalto futuro, así como al rociar la mezcla de betún calentada a una temperatura alta cuando entra humedad.
Todos los materiales suministrados a la planta se secan a una temperatura de 150 grados. La detección se lleva a cabo utilizando una pantalla. La carga mineral se muele en un molino hasta un estado en polvo. Dependiendo de la tecnología, el secado puede ser simple o doble. La eliminación de la humedad puede ocurrir después de la detección y la trituración.
Mezcla de componentes procesados
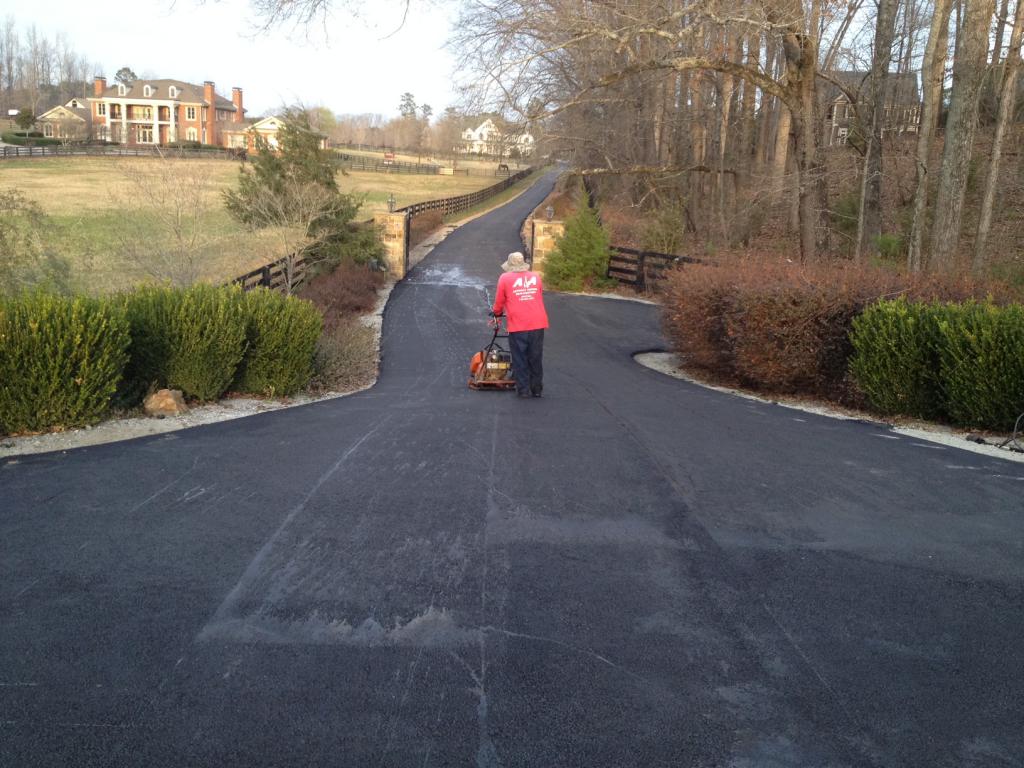
La piedra triturada y la arena después del procesamiento preliminar caen sobre el transportador, desde donde se transportan a la tolva, y luego se mezclan con betún. Después de eso, la temperatura en la tolva se incrementa a 160 grados y el contenido se deja en estado calentado para almacenamiento durante hasta 4 días. Si durante este período el material no se envía al consumidor, comenzará a perder sus características de resistencia.
Se añaden aditivos en asfalto y caucho desmenuzado a la mezcla terminada y calentada, lo que le da al material resistencia adicional y resistencia a factores externos.
Entrega de asfalto al lugar de colocación
El hormigón asfáltico se transporta por carretera hasta el lugar de instalación o reparación del pavimento de hormigón asfáltico. Muy a menudo, este material de construcción se transporta en camiones volquete que tienen un cuerpo resistente a los componentes calientes. Para el transporte de pavimento de hormigón asfáltico a largas distancias, se utilizan kochers (automóviles equipados con contenedores de ahorro de calor). En ellos, el asfalto mantendrá su temperatura inicial durante dos días después de la carga.
Control de calidad de carreteras
El concreto asfáltico debe cumplir con los GOST y SNiP establecidos adoptados en nuestro país. Se emite un certificado de cumplimiento de los documentos reglamentarios al fabricante solo después de pasar pruebas exhaustivas.
Hay varios laboratorios en Rusia que monitorean la calidad de las carreteras. Realizan un muestreo del pavimento de concreto asfáltico terminado y verifican el cumplimiento de varios parámetros.
En los estudios, se toma una muestra promediada de la masa total de hormigón asfáltico. Un análisis del camino ya construido se lleva a cabo examinando el núcleo (el llamado núcleo de asfalto). Se obtiene perforando la base de un pavimento de hormigón asfáltico utilizando un taladro hueco especial.
Aplicación de asfalto en frío
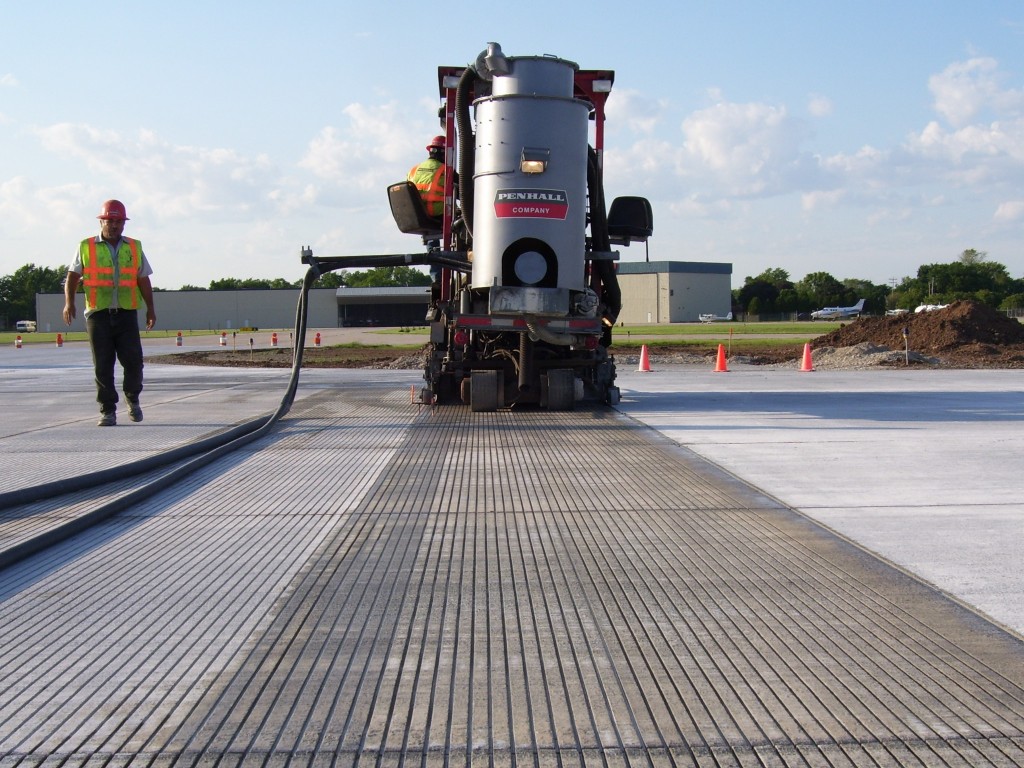
En aquellos lugares donde la entrega de materiales de construcción calientes para la reparación o construcción de la vía es imposible, se utiliza la colocación en frío del pavimento de hormigón asfáltico. La tecnología de tal construcción de carreteras se caracteriza por temperaturas de operación más bajas para calentar la mezcla (el asfalto se calienta a 100 grados). Para dar al camino suficiente resistencia, se usan composiciones de polímeros.
Antes de la colocación, los trabajadores calientan no solo el hormigón asfáltico, sino también el lugar de la colocación planificada. Dependiendo de la variedad, el camino se puede hacer incluso con heladas.
Una de las ventajas de la colocación en frío es la larga vida útil del material para la construcción de carreteras. A diferencia del concreto asfáltico ordinario, el asfalto resistente a las heladas se puede colocar después de algunas semanas. Sin embargo, este material tiene desventajas significativas, a saber:
- La resistencia es menos de 2 veces, en comparación con la clásica mezcla de asfalto.
- El material tiene un alto precio como resultado de agregar componentes protectores adicionales a su composición.
- La tecnología de colocación es complicada, lo que conduce a un aumento en el costo del pavimento.
- No soporta cargas pesadas.Está prohibido conducir vehículos que pesen más de 3.5 toneladas.
Se utiliza una placa vibratoria para apisonar el asfalto frío, y la colocación final se produce después de un momento en que durante la operación los automóviles se moverán a lo largo de la pista terminada, aplastando así el revestimiento.
Reutilizar asfalto
El alto costo de la construcción de carreteras ha llevado a los expertos a encontrar formas de ahorrar dinero. Una forma de reducir el costo de reparación y construcción de carreteras es reciclando, es decir, reciclando asfalto viejo para su reutilización. La superficie de la carretera adquiere una segunda vida después de procesar el material en recicladores móviles especiales.
¿Qué edad se recicla el asfalto?
El procesamiento de asfalto para obtener una nueva mezcla para la construcción de carreteras es un proceso de alta tecnología. Para producir un recubrimiento de alta calidad mediante reciclaje, debe:
- Corte el pavimento viejo con un remixer. Dicho equipo elimina suavemente una determinada capa de la carretera con un cortador especial.
- Moler la capa molida al tamaño de piedra triturada. El material resultante se llama "granulador". Se utiliza para reparar carreteras y preparar otras mezclas de construcción.
- Caliente el horno para derretir el granulador, y no debe usar fuentes de fuego abiertas, ya que puede ocurrir una explosión.
- Agregue betún y varios aditivos al horno, si la tecnología lo proporciona para la producción de nuevo asfalto.
Una tecnología como el reciclaje se utiliza, por regla general, para la construcción de carreteras en la ciudad. El asfalto reciclado tiene las mismas propiedades que el nuevo, pero su precio es mucho más bajo.
Mejora de la superficie de la carretera.
Las superficies de las carreteras se pueden modernizar con el tiempo. Uno de estos métodos es la aplicación de masilla en el asfalto. El material de refuerzo incluye betún y polímeros de caucho líquido.
Durante el funcionamiento, aparecen grietas en las carreteras donde puede entrar agua. Cuando se congela, se destruye el asfalto, lo que conduce a la formación de grandes pozos. Si aplica masilla a tiempo para eliminar las grietas, puede extender la vida útil del asfalto por varios años.
Ventajas y desventajas del asfalto.
El revestimiento de asfalto para el tráfico se ha utilizado durante varias décadas. Todavía no hay reemplazo para él, y he aquí por qué:
- El pavimento de asfalto no es muy costoso, especialmente si la carretera está diseñada para el transporte ligero.
- El asfalto resiste las heladas, no le teme a la humedad ni a las fuertes lluvias, por supuesto, si se siguen sus tecnologías de colocación.
- Si el recubrimiento se ha colapsado parcialmente, se puede reparar parcheando.
- En climas adversos, se puede utilizar la tecnología de asfalto frío.
Alternativas al asfalto
En el mundo, los científicos están trabajando para crear una alternativa más confiable y barata a la mezcla de concreto asfáltico, pero hasta ahora no se ha encontrado que ese material sea un competidor digno. Además, el pavimento de asfalto está en constante modernización. La introducción generalizada de nuevas sustancias poliméricas puede mejorar significativamente las propiedades de la superficie de la carretera y ampliar los límites de su aplicación. Esto se confirma mediante numerosas pruebas de laboratorio.
Construcción de hormigón asfáltico
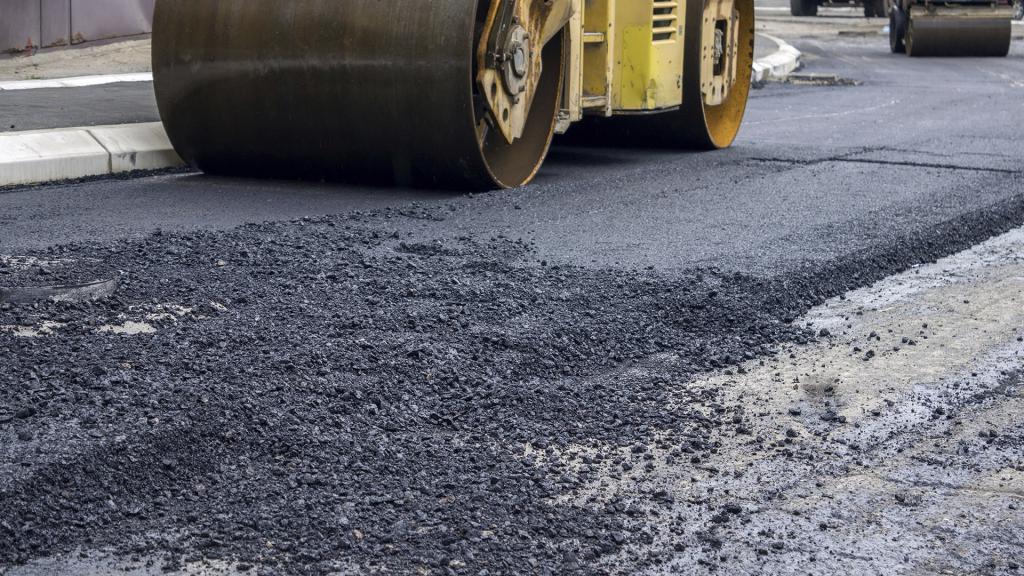
Los especialistas se esfuerzan por construir y construir carreteras de tal manera que haya la menor cantidad posible de capas en la carretera, hasta una. El concreto asfáltico se debe colocar preferiblemente directamente en el suelo. El número mínimo de capas reduce el tiempo de reparación del lienzo, facilita la organización de la construcción de nuevas carreteras, reduce la variedad de equipos necesarios para colocar el asfalto.
El diseño moderno del pavimento de hormigón asfáltico consta de las siguientes partes:
- Capa superior.
- La capa porosa inferior.
- Piedra triturada mezclada con aglutinantes.
- La base está hecha de grava o escombros.
- Capa de arena.
- Asfalto triturado.
Durante la construcción del pavimento de asfalto, se deben observar una serie de condiciones. Para una fuerte unión entre la capa superior de asfalto y la base, se aplica un material resistente a las grietas a partir de materiales tratados con betún con una altura de al menos 15 cm. El espesor del revestimiento de hormigón asfáltico que se coloca sobre la base de materiales minerales debe ser de al menos 5-6 cm.